Social responsibility in the supply chain
The manufacturing methods for producing our rugs range from from machine-made rugs in large volumes to unique rugs woven by hand by men and women in their homes. There are many methods used to produce the rugs we sell, and our suppliers are found mainly in Eurasia, the Middle East and Asia. To ensure that our high demands on human rights and working conditions are met, we work on several levels both locally and globally. Together with several independent interest groups, we carry out ongoing follow-ups and audits of our suppliers.
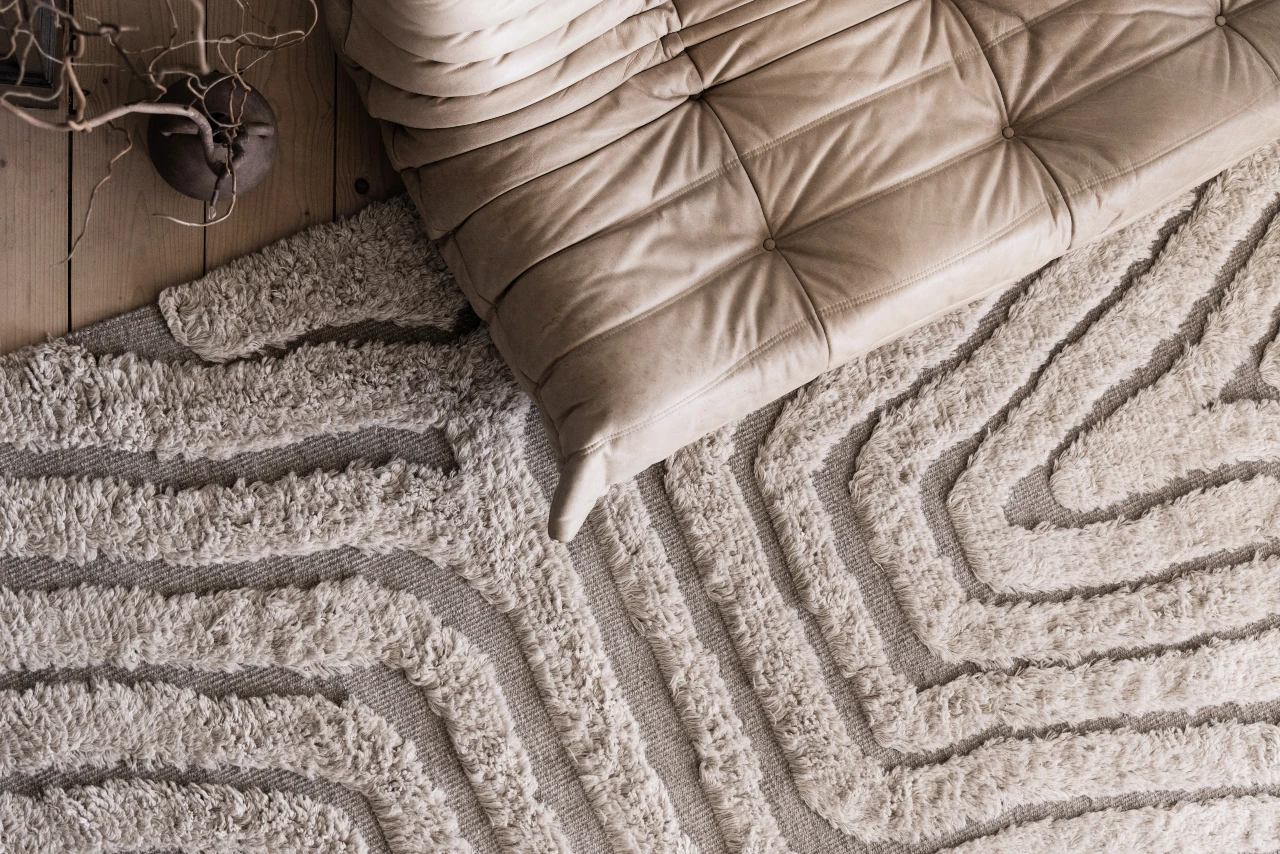
Sustainability includes people
Since sustainability for us also applies to people, we work on several fronts to ensure that our suppliers work responsibly and with respect for the people who manufacture the rugs.
We are primarily an online retailer of rugs, which means that we do not own any factories, instead we work with carefully selected suppliers in long-term partnerships. These close collaborations enable a regular dialogue, mutual commitment and joint development activities that contribute to a positive impact in the supply chain.
To take the lead in continuous improvement
There are many challenges when it comes to working conditions in production, mainly due to a lack of management systems. As one of the leading online trading venues for rugs, we can lead a continuous improvement and impact work to ensure that every worker in the supply chain is respected, has a safe workplace and a reasonable salary for their work..
We demand that our suppliers offer
- Opportunity for secure employment and a secure workplace
- Reasonable compensation for the work effort
- A workplace without discrimination where people feel respected and can express their opinions.
- Regular social audits to identify, manage and report risks, or consequences related to human rights. This process includes continuous dialogue to increase awareness and address risks when needed.
- Cooperation with NGO’s for long-term development in various areas such as women’s rights, occupational safety, and children’s right to schooling.
Human Rights
Our most fundamental responsibility is to respect and support human rights. This is a prerequisite for our business model to be sustainable in the long run and an important aspect of our values.
The most important issues related to human rights include fair compensation, the right to trade union membership and the right to collective agreements, but also include other human rights such as non-discrimination, integrity, and children’s right to schooling.
We have a code of conduct for suppliers, which follows the UN’s guiding principles for business and human rights. Risks related to human rights in the supply chain are identified and managed in the following steps:
- Regular social audits performed by accredited third-party auditors.
- Training in human rights, both for Rugvista’s employees and suppliers.
- Immediate action in the event of incidents for which we have communicated zero tolerance – with a special focus on human rights among suppliers, according to Label STEP’s and amphora BSCI’s protocol for zero tolerance.
Code of conduct for suppliers
We are members of the amfori Business Social Compliance Initiative (BSCI), which is an independent organization that reviews and designs industry regulations regarding work environment and human rights. By using their common code of conduct – amphora BSCI Code of Conduct – we want to ensure that our suppliers offer a safe working environment respecting and abiding international human rights and labor laws. The amfori BSCI Code of Conduct refers to international conventions, such as the Declaration of Human Rights, the United Nations Guiding Principles on Business, the OECD Guidelines, the UN Global Treaties and the International Labor Organization (ILO) conventions and recommendations for improving working conditions in supply chain.
Read the full code of conduct here
Supplier reviews and follow-ups
We work closely with and for continuous dialogue with our suppliers where we clarify our requirements. They, in turn, must communicate the requirements to their subcontractors and ensure that they also sign the amphora BSCI code of conduct. We review suppliers regularly, both through inspections carried out by our own staff and through independent third-party inspections, either carried out in accordance with amfori BSCI’s or Label STEPS ‘social audit systems. After an audit, we receive an audit report where any deviations are clarified. The suppliers that are audited through amphora BSCI’s system receive a status of A-E.
Review of home-woven rugs
Some of our rugs are woven or knotted at home, which is not an unusual extra income in some parts of the world. The suppliers whose rugs are manufactured by home weavers are audited by LabelSTEP, an independent non-profit organization that works to ensure fair trade of handmade rugs according to ten principles that include wages, health, discrimination, and inhuman treatment.
Zero Tolerance
In the event of incidents involving zero tolerance, we shall act immediately in accordance with Label STEP’s and amphora BSCI’s protocols for zero tolerance. Rugvista has never had such an incident, which is probably due to our close collaboration with our suppliers and with LabelStep and BSCI.
Upon review
In an audit, the supplier is examined by amfori BSCI or LabelSTEP based on the code of conduct. If a deviation is discovered and the deviation is not classified as zero tolerance, the supplier must produce an remediation plan to improve and remedy the found deviations. A follow-up audit takes place within 12 months from the moment the deviation was found.
If deviations persist, we enter into an in-depth dialogue with the supplier and discuss the requirements for continued cooperation.
Objective
Via amfori BSCI, suppliers are offered a comprehensive skills development program that includes employees’ rights, human rights, management systems, labor law issues, personal safety, the environment, and work with anti-corruption. The goal is for the suppliers themselves to take social responsibility for their production and their employees.
Our long-term goals:
- All our suppliers must undergo a full audit every year
- All suppliers included in amfori BSCI’s systems must achieve results A-C
- If the result at any point is C-E, a remediation plan must be drawn up
- In the event of incidents that are classified as zero tolerance, we act immediately